To właśnie od produkcji wysokiej jakości szprych zaczęła się historia firmy. Nazwa DT była synonimem wysokiej klasy szwajcarskich szprych jeszcze przed założeniem dzisiejszej firmy DT Swiss AG. Po dziś dzień szprychy DT Swiss oznaczają trwałość oraz precyzję i są niezrównane dzięki swojemu unikalnemu procesowi produkcji, gwarantującemu lekkość i wytrzymałość.
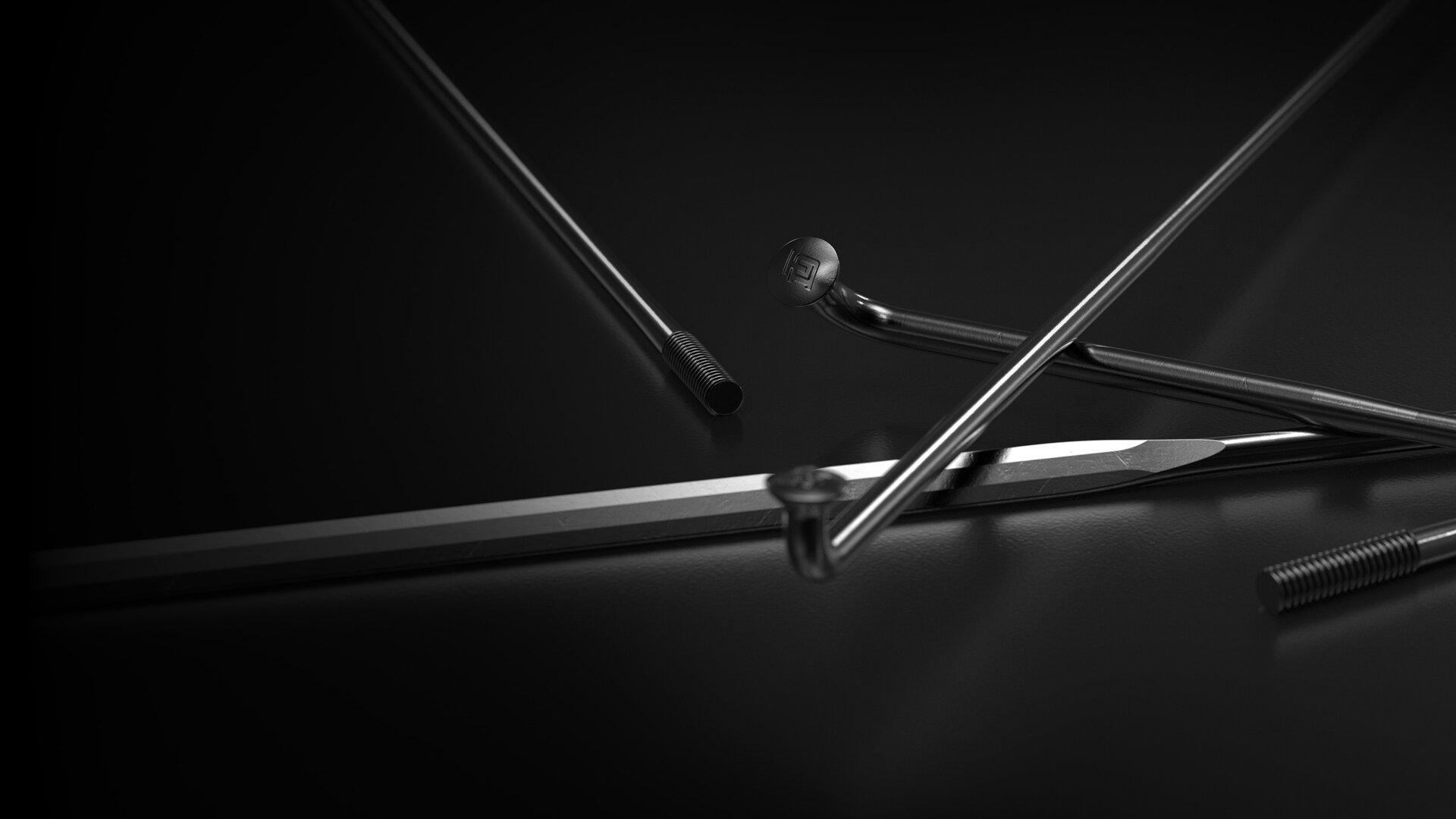
Technologia szprych
Produkcja szprych krok po kroku
Surowiec stalowy
Specjalnie przetworzony stop stali do produkcji szprych pochodzi od wyselekcjonowanych dostawców drutu. Surowiec musi mieć niezmiennie wysoką jakość, która jest kontrolowana przez cały czas.
Każda szprycha podlega pewnym zmianom, dlatego określony stop stali pozwala na dalszą obróbkę drutu w celu uzyskania wymaganej wytrzymałości i właściwości wydłużania. Od tego momentu kontrola jakości jest niezbędna, ponieważ dostarczony surowiec musi być zgodny ze specyfikacjami składu i jakości wymaganymi przez DT Swiss.
Drut
Dostarczony drut szprychowy ze stali nierdzewnej 18/10 przeszedł już testy zginania i rozciągania w odpowiednim dziale dostawcy. Drut szprychowy nawijany jest na szpule (zwoje) o masie ok. 800 – 900 kg i dostarczany w 4 różnych średnicach: 1.8, 2.0, 2.15 i 2.34 mm. Ścisła wymiana informacji i koordynacja kontroli produktów między DT Swiss a dostawcą drutu zapewnia utrzymanie wąskich tolerancji powierzchni, średnicy i owalności drutu. Przestrzeganie specyfikacji gwarantuje wydajną i przyjazną dla maszyn produkcję szprych. Proces kontroli towarów wychodzących po stronie dostawcy jest identyczny z kontrolą towarów przychodzących w DT Swiss. W celu skontrolowania gładkości powierzchni zwoju wystarczy po prostu dotknąć jej dłonią. Następnie kontroluje się średnicę i owalność za pomocą mikrometru.
Prostowanie szprych
Drut jest odwijany bezpośrednio ze zwojów i prostowany maszynowo, a następnie cięty na długość w celu utworzenia półfabrykatów szprych. Ta czynność jest wykonywana w przypadku wszystkich szprych, a w jej wyniku powstają proste półfabrykaty, precyzyjnie przycięte na długość do setnych części. W tym momencie najważniejsza kontrola dotyczy nie tylko materiału, ale również maszyny i jej zużycia. Każda maszyna produkcyjna podlega sprawdzeniu dwa razy dziennie za pomocą różnych narzędzi pomiarowych o wąskich tolerancjach, aby zapewnić stałą jakość i wykończenie materiału. Jest to bardzo ważna kontrola dla płynnego przebiegu kolejnych etapów przetwarzania.
Kucie na zimno
Proces ten, opracowany i opatentowany przez DT Swiss, jest wykorzystywany do zmniejszenia docelowej średnicy szprych. Oscylujące młotki obracające się wokół drutu ściskają półfabrykat, zmniejszając jego średnicę. W wyniku tego procesu powstaje szprycha zarówno lekka, jak i mocna, z cieniowaną elastyczną częścią zapewniającą lekkość oraz mocniejszą główką i gwintem w celu zwiększenia nośności.
Dzięki zastosowaniu kucia na zimno materiał jest wzmacniany przy zachowaniu dobrych właściwości wydłużania. Przejście od zredukowanej do niezredukowanej średnicy szprychy jest niezwykle harmonijne i zapewnia wygląd wysokiej jakości. Przed następnym krokiem obróbki wybrane szprychy są sprawdzane ręcznie pod kątem prostoliniowości, średnicy i owalności.
Formowanie główki i gwintu
W miarę postępu procesu wygląd produktu zaczyna zbliżać się do swojej znanej postaci. Następuje cięcie szprych na dokładnie obliczony i pożądany wymiar. Zaraz po nim następuje tłoczenie główki szprychy z unikalnym symbolem „DT”. Szprychy o klasycznym kształcie są dodatkowo wyginane pod kątem 90–95°. Na drugim końcu szprychy w procesie walcowania formowany jest gwint. Zapewnia to prawidłową długość, kształt litery J w przypadku klasycznych szprych i prowadzi do wzmocnienia materiału na gwincie, co upraszcza konstrukcję koła i zwiększa wytrzymałość.
Następnie przeprowadza się kilka kontroli szprych. Kontrola optyczna główki szprychy gwarantuje, że logo jest widoczne, a materiał nie ma wad na zagięciu. Średnicę główki, długość zagięcia i gwint (jego długość i średnicę) mierzy się za pomocą suwmiarki cyfrowej. Gwint szprychy przechodzi ręczny test działania. Ostatnim pomiarem jest pomiar punktu zerowego za pomocą wysokościomierza Trimos. Taka seria testów jest wykonywana co 35 minut na co najmniej jednym egzemplarzu szprychy.
Kucie płaskie
Materiałem źródłowym są szprychy mające stały przekrój lub kute na zimno, które podczas tego procesu są spłaszczane masą do 200 ton. Ten płaski kształt szprychy zapewnia w szczególności korzyści aerodynamiczne. Proces kucia jeszcze bardziej zagęszcza materiał, co z kolei pozwala uzyskać większą wytrzymałość. Każda szprycha jest sprawdzana pod kątem prawidłowej długości i jej płaskiej części – taka kontrola jakości odbywa się co 15 minut.
Czernienie szprych
Ze względów estetycznych szprychy mogą być również poczernione. Chociaż może się to wydawać proste, proces czernienia jest dość szczególny. Ma na celu zagwarantowanie zabarwienia szprych bez wpływu na wagę i osiągi. W ramach każdego zamówienia wybrane szprychy są testowane pod kątem jakości zaczernienia, aby zapewnić optymalną odporność nawet po kilku latach. Około 85% wytwarzanych szprych opuszcza zakład w kolorze czarnym.