C’est avec la production de rayons de haute qualité que l’entreprise a commencé son activité. DT était le synonyme de rayons suisses de qualité supérieure, même avant la création de l’entreprise actuelle DT Swiss AG. Aujourd’hui encore, les rayons DT Swiss sont synonymes de longévité et de précision. Leur processus de production exclusif qui allie légèreté et longévité leur procure une qualité inégalée.
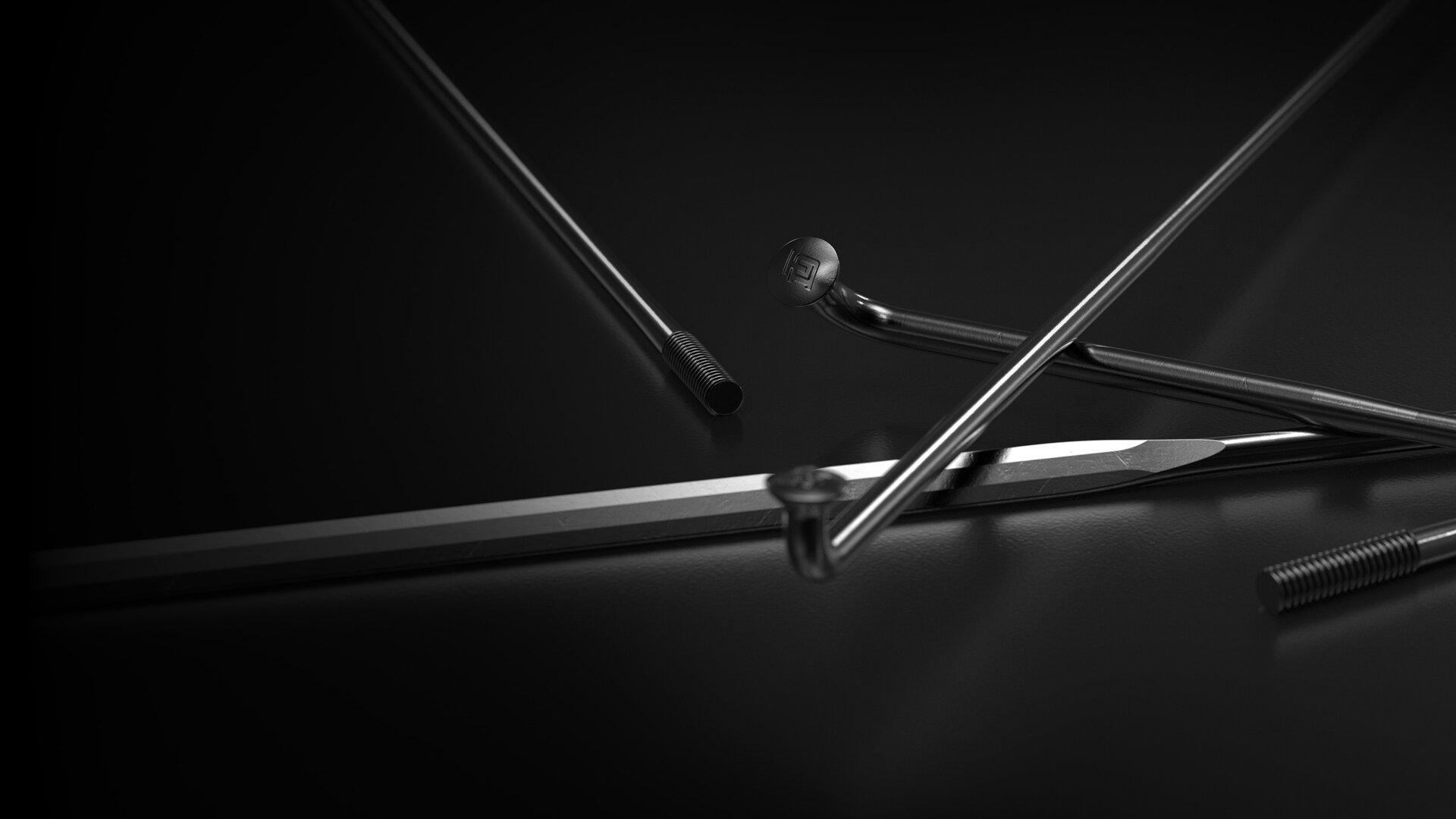
technologie
rayons
La fabrication de vos rayons étape par étape
Matière première : l’acier
L’alliage d’acier spécialement traité pour la fabrication des rayons provient de fournisseurs de fils d’acier sélectionnés. Cette matière première doit être de haute qualité constante qui est contrôlée en permanence.
Un rayon subira un certain nombre d’altérations, c’est pourquoi un alliage spécifique de l’acier permet de transformer le fil pour obtenir les propriétés de résistance et d’allongement requises pour la fabrication du rayon. À partir de là, le contrôle de la qualité est essentiel. La matière première livrée doit être conforme aux spécifications exigées par DT Swiss concernant sa composition et sa qualité.
Matière première : le fil d’acier
Le fil de rayon livré en acier inoxydable 18/10 a déjà subi des tests de flexion et de traction chez le fournisseur. Le fil de rayon est enroulé en bobines d’environ 800 - 900 kg et est livré en 4 diamètres différents : 1.8, 2.0, 2.15 et 2.34 mm. Les échanges et la coordination étroite entre le contrôle produit de DT Swiss et celui du fournisseur de fil d’acier, garantissent le respect des tolérances très strictes en termes de surface, de diamètre et d’ovalisation du fil. Le respect des spécifications permet de garantir une production de rayons efficace et adaptée aux machines. Le contrôle des produits au départ du fournisseur est identique à celui effectué à l’arrivée chez DT Swiss. Afin d’assurer une surface lisse, c’est par un simple toucher de la main que les tests sont effectués, sur la surface de la bobine. Le diamètre et l’ovalisation sont ensuite contrôlés avec un micromètre.
Rectification des rayons
Le fil est déroulé directement des bobines et rectifié à la machine puis coupé à la bonne longueur pour former les ébauches de rayons. Cette étape est effectuée pour tous les rayons et permet d’obtenir des ébauches de rayons droites, coupées à la bonne longueur avec une précision de l’ordre du centième. Ici, le contrôle le plus important n’est pas seulement effectué sur le matériau, mais aussi sur la machine et son usure. Chaque machine de la production est vérifiée deux fois par jour à l’aide de différents outils de mesure aux tolérances très strictes afin de garantir une qualité et une finition constantes du matériau. Ce contrôle est très important pour le bon déroulement des étapes suivantes.
Forgeage à froid
Ce procédé développé et breveté par DT Swiss est utilisé pour réduire le diamètre des rayons. En faisant tourner des marteaux oscillants autour du fil, l’ébauche de rayon est comprimée et son diamètre réduit. Ce procédé permet d’obtenir un rayon à la fois léger et solide, avec une partie élastique aboutée pour la légèreté et une tête et un filetage plus fermes pour une plus grande capacité de charge.
Le processus de forgeage à froid permet de renforcer le matériau tout en conservant ses bonnes propriétés d’allongement. La transition entre le diamètre réduit et le diamètre non réduit d’un rayon est extrêmement harmonieuse et crée une apparence de haute qualité. Avant l’étape suivante, une sélection de rayons est contrôlée à la main pour vérifier leur rectitude, leur diamètre et leur ovalisation.
Fabrication de la tête et du filetage
Au fur et à mesure des étapes, le produit se rapproche de sa forme connue. Les rayons sont coupés à la dimension exacte calculée et souhaitée. La tête de rayon est ensuite immédiatement embossée avec le symbole exclusif « DT ». Les rayons classiques sont en outre coudés selon un angle de 90 à 95°. À l’autre extrémité de l’ébauche de rayon, le filetage est formé selon un processus de roulage. Cela permet d’obtenir la bonne longueur, la forme en J des rayons classiques et un renforcement du matériau sur le filetage, ce qui simplifie la construction de la roue et augmente la résistance.
Plusieurs contrôles sont ensuite effectués sur les rayons. Un contrôle optique de la tête du rayon permet de s’assurer que le logo est visible, et que le matériau ne présente aucun défaut sur son angle. Le diamètre de la tête, la longueur de l’angle et le filetage (longueur et diamètre) sont mesurés à l’aide d’un calibre numérique. Le filetage du rayon est soumis à un test de fonctionnement manuel. La dernière mesure est une mesure du point zéro avec un altimètre Trimons. Cette série de tests est effectuée toutes les 35 minutes sur au moins un rayon.
Forgeage à plat
Le matériau de base est constitué par des rayons plats ou forgés à froid, qui sont aplatis au cours de ce processus avec un poids pouvant atteindre 200 tonnes. Cette forme plate du rayon offre des propriétés aérodynamiques particulièrement intéressantes. Le processus de forgeage densifie encore plus le matériau, ce qui permet d’obtenir une plus grande résistance. Une inspection de chaque rayon est effectuée pour s’assurer qu’il a la bonne longueur et pour contrôler sa partie plate. Ce contrôle de qualité est effectué toutes les 15 minutes.
Noircissement des rayons
Pour des raisons esthétiques, les rayons peuvent également être noircis. Bien que cela puisse paraître simple, ce processus de noircissement est assez spécifique pour garantir que la coloration des rayons n’ajoute pas de poids supplémentaire ou ne pénalise pas les performances. Pour chaque commande, une sélection de rayons est testée sur la qualité du noircissement afin de garantir une résistance optimale même après plusieurs années. Environ 85 % des rayons qui sortent de l’usine sont noirs.